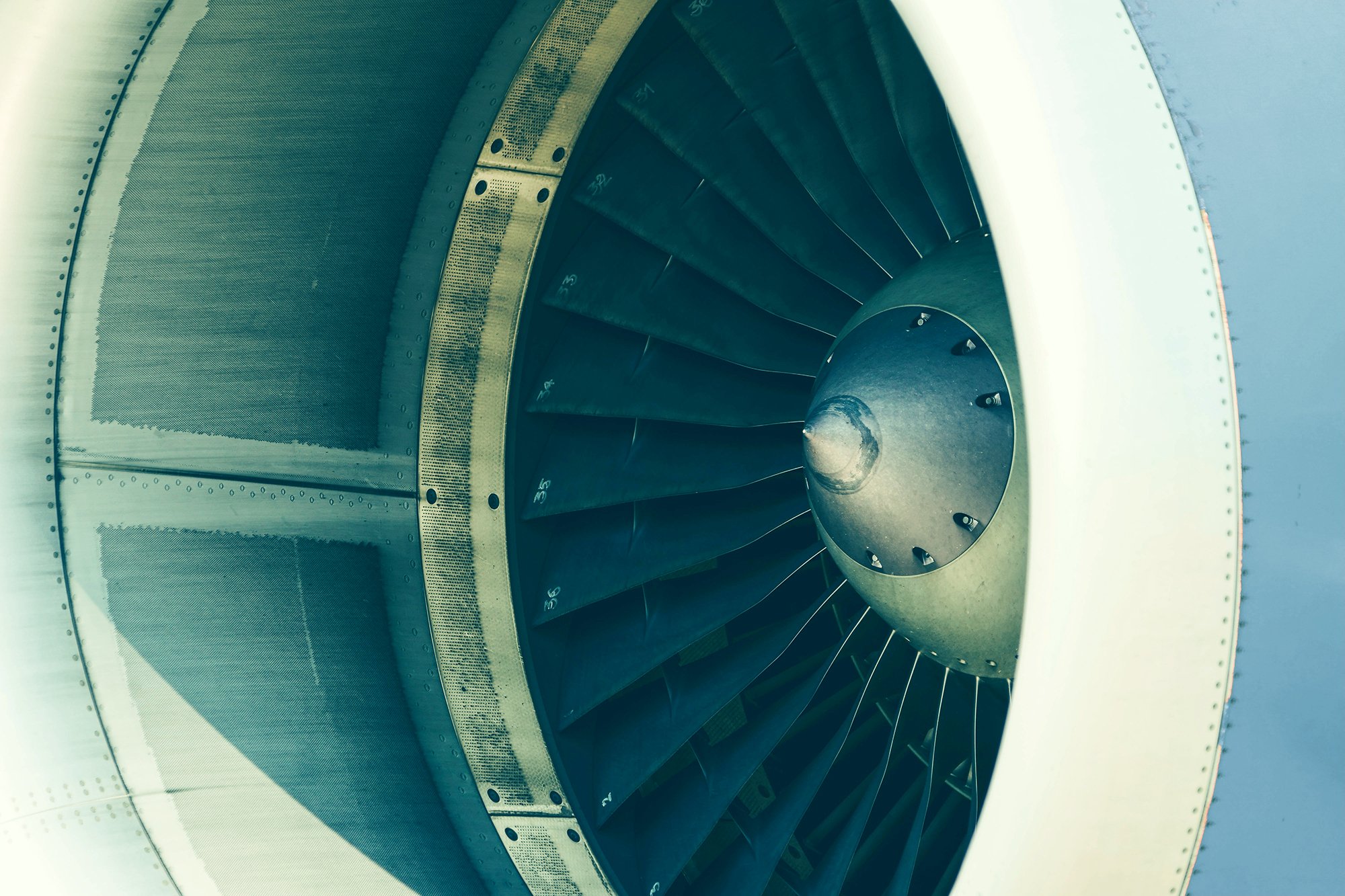
Project concept
HESTIA specifically focuses on increasing the scientific knowledge of the hydrogen-air combustion of future hydrogen-fuelled aero-engines.
Highlights
5
MILLION EUROS FROM HORIZON EUROPE
48
MONTHS’ DURATION
18
UNIVERSITIES AND RESEARCH CENTRES
6
EUROPEAN AERO-ENGINE MANUFACTURERS
Abstract
To reduce climate impact of aviation, decarbonisation is a major challenge. Current combustion chambers are burning hydrocarbon fuels, such as kerosene or, more recently, emerging SAF products.
Hydrogen is also considered a promising energy carrier, but the burning of hydrogen creates radically new challenges which need to be understood and anticipated.
HESTIA specifically focuses on increasing the scientific knowledge of the hydrogen-air combustion of future hydrogen-fuelled aero-engines.
The related physical phenomena will be evaluated through the execution of fundamental experiments. This experimental work will be closely coupled to numerical activities which will adapt or develop models and progressively increase their maturity so that they can be integrated into industrial CFD codes.
Improvement of the scientific understanding of hydrogen-air turbulent combustion: preferential diffusion of hydrogen, modification of turbulent burning velocity, thermoacoustics, NOx emissions, adaptation of optical diagnostics;
Assessment of innovative injection systems for H2 optimised combustion chambers: flashback risk, lean-blow out, stability, NOx emission minimisation, ignition;
Improvement of CFD tools and methodologies for numerical modelling of H2 combustion in both academic and industrial configurations.
HESTIA gathers 18 universities and research centres, as well as 6 European aero-engine manufacturers, to significantly prepare, in a coherent and robust manner, for the future development of environmentally friendly combustion chambers.
Different challenges are to be addressed in HESTIA project in a wide range of topics:
Objectives
With the overarching ambition of increasing the knowledge base and developing basic numerical models of performance and behaviour supported by experimental results, the HESTIA project has the following three objectives:
Objective_One
Further the understanding of H2/air combustion through elementary lab scale testing and basic modelling of specific phenomena
Objective_Two
Develop experimental capabilities and improved modelling methodologies for detailed assessment of H2/air characteristics in more representative aeronautical conditions
Objective_Three
Benchmark the performance of incremental and breakthrough injection systems concepts and identify the most relevant concepts
Work plan structure
To achieve its aims, the project is broken into five Work Packages (WPs), the first three WPs tackling the technical understanding and developing the technologies, and the other two dealing with exploitation/ dissemination and project management.
-
Understand the mechanisms involved in flame stabilisation
Identify the routes responsible for nitrogen oxide formation
Predict and control thermo-acoustic instabilities
Analyse the influence of film cooling on the flame properties
Develop an experimental database
Develop turbulent combustion models for CFD adapted to aeronautical combustors.
-
Experimental investigation of H2 combustion with different mix levels with CH4 and different premixed levels
Numerical simulations to capture the effects of mixedness with H2 combustion
Design of an optimised H2 mixer with regard to NOx emissions and safety margins with regards to flashback and autoignition
Experimental investigation of strut injectors for micromixing while preserving thermal resistance of the walls
Investigation of novel fuel injection technologies based on distributed/multi-point injection
-
Numerical assessment and optimisation of H2 injector concepts within practical combustor configurations and aero engine representative conditions using validation data from previous WPs and WP3
Low TRL testing (up to TRL3) of H2 injector concepts at atmospheric, elevated pressure and low pressure (altitude relight like) conditions to characterise NOx vs. stability/operability trade
Evaluation of the relative performance benefits and risks for aircraft application
Define TRL6 roadmap for the maturation of most promising technologies and their application to future product
-
Coordinate the HESTIA project and provide the management structures to ensure a smooth run and the achievement of objectives.
Monitor the project’s progress and management of resources in line with the Financial Guidelines.
Ensure that the Consortium’s contractual duties are carried out in line by advising and guiding the participants to comply with EU regulations and their contractual and legal requirements.
-
Ensure that the knowledge and results obtained in HESTIA project are widely communicated within the scientific and aeronautical community, and to prepare their scientific and commercial exploitation.
Monitor the project results with regards to intellectual property to ensure proper protection for later commercial use.
Impact
Target groups
Scientific community
(Gas turbine) Engine manufacturers
Aircraft and other transport manufacturers
Airport authorities / Airport operators / ACI
Policymakers (DG ENER, DG MOVE, EP TRAN Committee, ITRE, IEA, ICAO)
Civil aviation authorities / Regulatory and certifying bodies
Airlines / Ground handling operators / Ground service providers (GSP)
LH2 tank developers & manufacturers
Needs addressed
Understanding of key phenomena of H2/air combustion in aircraft engines and its related influencing parameters remains unmastered today within the European aviation sector.
Robust experimental results and numerical models to be able to further design and develop the combustion chamber, ensuring: a safe burning process with guaranteed flame stability; an efficient overall performance and operability of the whole engine over a range of operating conditions; an acceptable level of non-CO2 emissions.
Testing use of H2 in aircraft turbomachinery, covering all critical points of target application.
-
Partially premixed turbulent confined H2/air burner
LEAF burner
High-pressure burner for strut injectors
RQL injector burner apparatus
H2 planar jet flame in air co-flows
2D planar stratified H2 combustion
-
Atmospheric gas turbine model combustor
Low-TRL concepts for H2 injector and combustion systems developed and validated
Cross-comparison and selection of recommended optimized H2 injection concepts including risk evaluation
Roadmap to mature H2 injection technology to TRL6 by 2028
-
Sector burner test rig
Low-pressure test rig
Higher TRL test benches
Expected results
Outcomes (medium term)
Engine manufacturers to address learnings from HESTIA in the development of future aero engines and industrial gas turbine products, including MRO activities
Engine manufacturers to file patents on innovative H2 combustion devices
Further maturation of results within the Rolls-Royce University Technology Centre (UTC) network
Strengthening of industry-research networks in the area of H2 combustion
Impact (long term)
Mature H2 injection technology to TRL6 by 2028
Through the reduction of non-CO2 emissions, reduce climate impact in flight by 50-75 %.
Open up new target markets for regional and SMR aircraft manufacturers and for LH2 tank suppliers